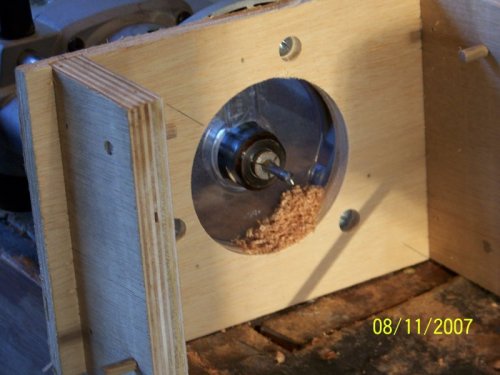
|
I
used a 1/4 inch straight bit initially to "rough out" the
blank. Because the bit wasn't long enough, I used an extension
collet to get the length I needed. The collet was made by CMT
(part #796.001.00) and a 1/2 to 1/4 in collet reducer (from Eagle
Hardware). The depth was set on the face of the leg blank as this
would have cut shoulders. The profile was cut based a section
through the center across the flats. For sloped corners, the
profile would be based on a diagonal section and the bit depth set to
the corner.
|
|
It is easier to control the router
using a climb cut as the router is moved along the jig. This
means the edge being cut, is moving the same direction as the bit is
turning. If you are taking too big a bite, it can actually spin
the blank faster. The router is very hard to control, if you try
to move it against the direction of the bit. The bit can dig in,
and ruin the blank.
I used the straight bit until I got to within one inch of the final
diamters. I then continued using the straight bit to cut the
straight areas of the leg, leaving a buffer area between the detailed
area and the straight area. This produces a smoother cut.
|
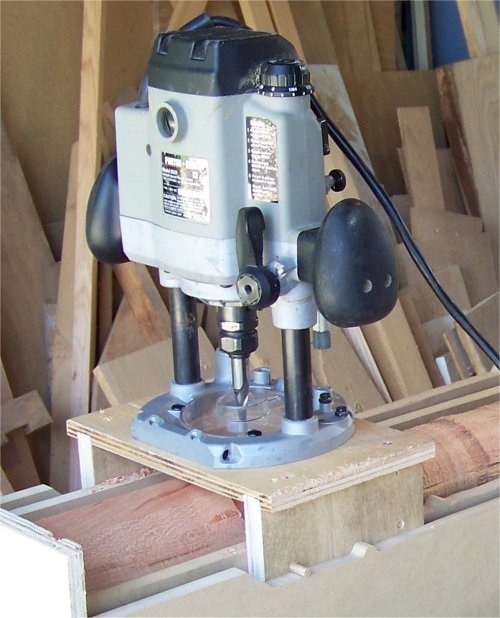
|
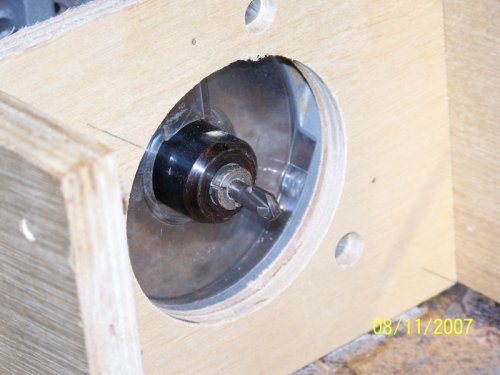
|
After
I cut the straight areas to the final diameter, I changed to a pointed
bit to cut the detailed areas. I would move the router from right
to left (climb cutting) for most of the cut, but would work from the
high areas to the lower areas to clean up the cut. After all the
cutting had been done with the router, I used a sharp, straight chisel
to smooth the finished blank before sanding.
|
|
|